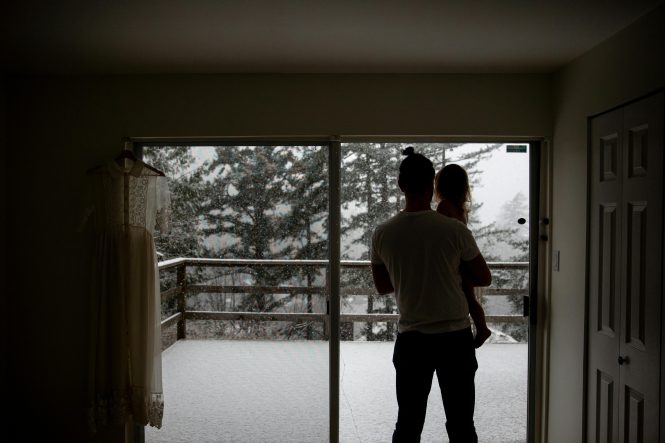
Dealing with cold room feels is a common challenge faced by businesses relying on cold storage solutions. Uncomfortable cold temperatures can disrupt operations, lead to product spoilage, and ultimately impact profitability. This article delves into the multifaceted problem of cold room feels and offers practical strategies to manage and minimize this issue. Dealing with cold room feels requires a nuanced approach that considers multiple factors, from insulation to ventilation. This comprehensive guide will explore various strategies, empowering you to craft a comfortable and efficient cold room, and we’ll cover the crucial aspects of design, maintenance, and temperature control. By the end of this article, you’ll be able to effectively address cold room discomfort and optimize your cold storage for maximum efficiency and comfort.
Understanding the Root Causes of Cold Room Discomfort
Understanding the causes behind cold room discomfort is the first step towards effective solutions. Various factors can contribute to unpleasant temperatures, from inadequate insulation to faulty refrigeration systems. Identifying the root cause ensures that the right solutions are implemented to create a comfortable and productive environment. Issues like improper insulation can lead to significant heat loss, resulting in a colder-than-desired temperature in the cold room. Poor ventilation, on the other hand, can lead to stagnant air and temperature fluctuations. We will delve into the nuances of each factor in detail to help you pinpoint the specific cause of your cold room discomfort.
Optimizing Cold Room Insulation for Temperature Regulation
Evaluating Current Insulation Methods
Proper insulation plays a vital role in maintaining a stable temperature within the cold room. Insulation acts as a barrier against heat transfer, preventing the cold air from escaping. Assessing the existing insulation is essential, considering its thickness, material type, and overall condition. Thin or damaged insulation will allow more heat transfer, driving up energy costs and creating a less-than-optimal temperature in your cold room. Regular inspections are critical to identify potential issues and implement necessary repairs or replacements.
Upgrading Insulation for Enhanced Efficiency
Upgrading insulation materials and methods can significantly improve temperature control. Choosing high-performance insulation materials, such as polyurethane foam or expanded polystyrene, can reduce heat transfer more effectively. In addition to material improvements, strategic placement and sealing of insulation in gaps and cracks can dramatically reduce heat loss and contribute to energy savings. Implementing new insulation techniques, such as specialized panels or vapor barriers, further boosts the insulation’s efficiency. Careful attention to detail is paramount for maximizing insulation effectiveness.
Fine-tuning Refrigeration Systems for Consistent Temperature
Regular Maintenance and Calibration
Regular maintenance is key to keeping the refrigeration system in top condition. Refrigerant leaks, compressor malfunctions, and dirty condenser coils can all disrupt temperature stability. Calibration of temperature sensors and regular inspections of the entire refrigeration unit are critical for identifying and resolving issues quickly. A well-maintained refrigeration system contributes to precise temperature control and minimizes temperature fluctuations.
Improving Air Circulation to Maintain Even Temperature
Addressing Airflow Barriers
Cold room layout and design significantly impact air circulation. Obstructions, like heavy equipment or improperly placed pallets, can impede airflow and create temperature gradients. This results in inconsistent temperatures in different areas of the cold room. Analyzing the layout and removing any obstacles or restructuring the layout will increase the circulation within the cold room.
Implementing Monitoring Systems for Real-time Temperature Tracking
Data-driven Insights for Optimization
Implementing a real-time temperature monitoring system provides valuable data for understanding temperature patterns and identifying potential issues. Data on temperature fluctuations, humidity levels, and other critical parameters can help pinpoint areas of concern within the cold room. Furthermore, remote monitoring allows managers to proactively identify any anomalies and take corrective actions promptly.
How can I choose the right type of insulation for my cold room?
The ideal insulation material depends on specific cold room requirements. Factors to consider include the desired temperature range, environmental conditions, budget, and the potential impact on the cold chain. Consult with experts and contractors to determine the most cost-effective and appropriate insulation for your cold room based on these considerations.
Frequently Asked Questions
What are the typical causes of inconsistent temperatures in cold rooms?
Inconsistent temperatures in cold rooms can stem from a variety of factors, including inadequate insulation, issues with refrigeration systems, insufficient air circulation, and improper cold room design. These elements contribute to uneven temperature distributions. Addressing these aspects is crucial for maintaining a stable and comfortable environment.
In conclusion, dealing with cold room feels involves a multi-faceted approach. Understanding the causes, implementing proper insulation, optimizing refrigeration systems, and maintaining a suitable environment are all crucial steps. By adopting these strategies, you can create a more comfortable and efficient cold room that meets your specific needs. To learn more about specific solutions, check out our guide on designing the ultimate cold room or visit our resources page for tips on reducing cold room issues. Do you have additional questions about dealing with cold room discomfort?